برش لیزری چیست؟
برش لیزری یک روش برش مواد است که از یک جریان نور متمرکز و منسجم استفاده می کند. این یک فرآیند کسری است که مواد را در طول فرآیند برش با استفاده از بخار، ذوب، ابلیشن شیمیایی یا انتشار ترک کنترل شده حذف می کند. نوری لیزری که توسط کنترل عددی کامپیوتری (CNC) کنترل می شود می تواند سوراخ هایی به اندازه 5 مایکرون سوراخ کند. این فرآیند هیچ تنش باقی مانده ای بر روی مواد ایجاد نمی کند و امکان برش مواد شکننده و شکننده را فراهم می کند. از زمان اختراع خود در اوایل دهه 1960، برش لیزری جایگاه خود را در صنایعی مانند الکترونیک، پزشکی، هوافضا، خودروسازی و نیمه هادی ها پیدا کرده است. یکی از رایج ترین کاربردها برای برش فلز – اعم از تنگستن، فولاد، آلومینیوم، برنج یا نیکل – است زیرا لیزرها برش های تمیز و پرداخت های صاف را ارائه می دهند. لیزرها همچنین برای برش چوب، شیشه، کاغذ، فلز، پلاستیک و حتی برخی از سنگ های قیمتی عالی هستند. برای افزودن به تطبیق پذیری آنها، هیچ ابزار خاصی برای تولید طرح های پیچیده تر مورد نیاز نیست.
تئوری برش لیزر و اصل کار
ليزر مخفف “تضخيم نور توسط تشعشع محرک شده” است. جدا از کاربردهای برش لیزر، آنها برای پیوستن، درمان حرارتی، بازرسی و تولید فرم آزاد استفاده می شوند. برش لیزری با سایر فرآیندهای ماشینکاری لیزری متفاوت است زیرا به تراکم قدرت بالاتر اما زمان تعامل کوتاه تر نیاز دارد..
لیزرها توسط یک منبع نور با شدت بالا در داخل یک حفره لیزری بازتابی تولید می شوند که حاوی یک میله لیزری است که تابش را تولید می کند. منبع نور باعث تحریک اتم های عصای لیزر می شود زیرا طول موج نور را از منبع نور جذب می کنند. نور از توده های کوچکی از فوتون ها تشکیل شده که به اتم های رسانه ای دائمی برخورد می کنند و آنها را انرژی می دهند. اتم های پرانرژی فوتون، دو فوتون دیگر با طول موج، جهت و فاز مشابه، که انتشار تحریک شده نامیده می شود، منتشر می کنند. فوتون های جدید، اتم های پر انرژی دیگر را تحریک می کنند و فوتون های بیشتری تولید می کنند، که باعث ایجاد یک سلسله هیجانات می شود. فوتون ها عمودی به آینه های موازی که در انتهای میله لیزر قرار دارند حرکت می کنند اما در داخل میله لیزر باقی می مانند. یک آینه انتقال دهنده است و اجازه می دهد تا بخشی از نور از حفره خارج شود. این جریان فرار از نور منسجم و تک رنگ، پرتو لیزری است که برای برش مواد استفاده می شود. مجموعه ای دیگر از آینه ها یا فیبر نوری نور را به یک لنز هدایت می کنند که نور را به مواد متمرکز می کند. سه نوع اصلی لیزر که برای برش استفاده می شود، لیزر CO2، Nd-YAG و لیزر فیبر نوری هستند. آنها در مواد مورد استفاده برای تولید پرتو لیزر متفاوت هستند.
لیزرهای فیبر با توجه به مخلوط منبع لیزرهای خود متفاوت هستند، از جمله ایتربیوم، تولیوم و اربیوم. انتخاب مخلوط بستگی به کاربرد و طول موج آن ها دارد. به عنوان مثال، اربیوم نور را در محدوده 1528nm تا 1620nm تولید می کند. یتربیوم نور با طول موج 1030 نانومتر، 1064 نانومتر و 1080 نانومتر تولید می کند. لیزر فیبر نوری در دو حالت تک و چندگانه هستند که قطر هسته لیزرهای تک حالته بین 8 تا 9 میکرون است در حالی که لیزرهای چند حالته دارای قطر 50 میکرون تا 100 میکرون هستند. از بین دو حالت، لیزرهای تک حالته کارآمدتر هستند و پرتو نور با کیفیت بهتری تولید می کنند. لیزرهای فیبر نوری به عنوان حالت جامد طبقه بندی می شوند زیرا منبع تغذیه آنها شیشه سیلیکا مخلوط با عناصر خاکی کمیاب است. این برخلاف لیزرهای CO₂ است که از گاز برای ایجاد قدرت خود استفاده می کنند. یک تفاوت اضافی بین این دو شکل توان، طول موج آنها است، به طوری که لیزرهای فیبر نوری طول موج های 780 نانومتر تا 2200 نانومتر تولید می کنند در حالی که لیزرهای CO₂ دارای طول موج های 9600 نانومتر تا 10600 نانومتر هستند.
لیزر فیبر نوری
لیزرهای فیبر نوری جدیدترین و محبوب ترین انواع لیزر هستند زیرا می توانند طول موج های مختلفی را برای برش دقیق تر تولید کنند. از یک کابل فیبر نوری ساخته شده از شیشه سیلیکا برای هدایت نور استفاده می کنند. پرتو لیزری که توسط لیزرهای فیبر نوری تولید می شود دقیق تر است زیرا مستقیم تر و کوچکتر است.
لیزرهای CO2
این نوع دارای یک محیط لیزری تخلیه گازی است که با 10 تا 20٪ دی اکسید کربن، 10 تا 20٪ نیتروژن کار می کند، که از هیدروژن و زنون و هلیوم برای تعادل استفاده میشود. به جای نور، پمپاژ لیزر با تخلیه یک جریان الکتریکی انجام می شود. هنگامی که تخلیه الکتریکی از طریق محیط لیزری عبور می کند، مولکول های نیتروژن تحریک می شوند و آن را به سطح انرژی بالاتر می برند. برخلاف آنچه قبلاً توضیح داده شد ، این مولکول های نیتروژن هیجان زده انرژی خود را با انتشار فوتون از دست نمی دهند. در عوض، انرژی حالت ارتعاش خود را به مولکول های CO2 منتقل می کند. این فرآیند تا زمانی ادامه می یابد که بیشتر مولکول های CO2 در حالت فراپایدار قرار بگیرند. مولکول های CO2 سپس نور مادون قرمز را با 10.6 یا 9.6 میکرو متر منتشر می کنند که آنها را به سطوح انرژی پایین تر می رساند. آینه های طنین دهنده برای بازتاب فوتون های ساطع شده در این طول موج طراحی شده اند. یک آینه بازتابنده جزئی است که اجازه می دهد پرتو مادون قرمز که برای برش مواد استفاده می شود آزاد شود. پس از آزاد کردن نور مادون قرمز، مولکول های CO2 با انتقال انرژی باقی مانده به اتم های هلیوم، به حالت اولیه باز می گردند. اتم های هلیوم سرد سپس گرم می شوند که توسط سیستم خنک کننده لیزر خنک می شوند. کارایی لیزر CO2 حدود 30 درصد است که بالاتر از سایر لیزرها است.
لیزرهای کریستالی (روبی، Nd و Nd-YAG)
بر خلاف لیزر CO2، این نوع لیزر حالت جامد است که از یک کریستال مصنوعی به عنوان یک محیط لیزری استفاده می کند. محبوب ترین آن، کریستال YAG است که با 1% نئودیمیوم یونیزه شده است. یون های Nd جای یون های Y را در ساختار کریستالی می گیرند. طول میله حدود 4 اینچ با قطر 2.4 تا 3.5 اینچ است. انتهای میله YAG با مواد بسیار بازتابنده ای که به عنوان سیستم رزوناتور عمل می کنند، پالش شده و پوشش داده شده است. پمپاژ لیزر با فلاش کریپتون یا دیود لیزر انجام می شود. این پمپ لیزر، یون های Nd را به سطوح انرژی بالاتر تحریک می کند. بعد از مدت کوتاهی، یون های Nd هیجان زده به حالت پایین تر و پایدارتر بدون انتشار فوتون ها حرکت می کنند. این فرآیند تا زمانی ادامه می یابد که محیط با یون های Nd هیجان زده پر شود. از حالت فراپایداری خود، یون های Nd نور مادون قرمز با طول موج 1064 نانومتر را آزاد می کنند.
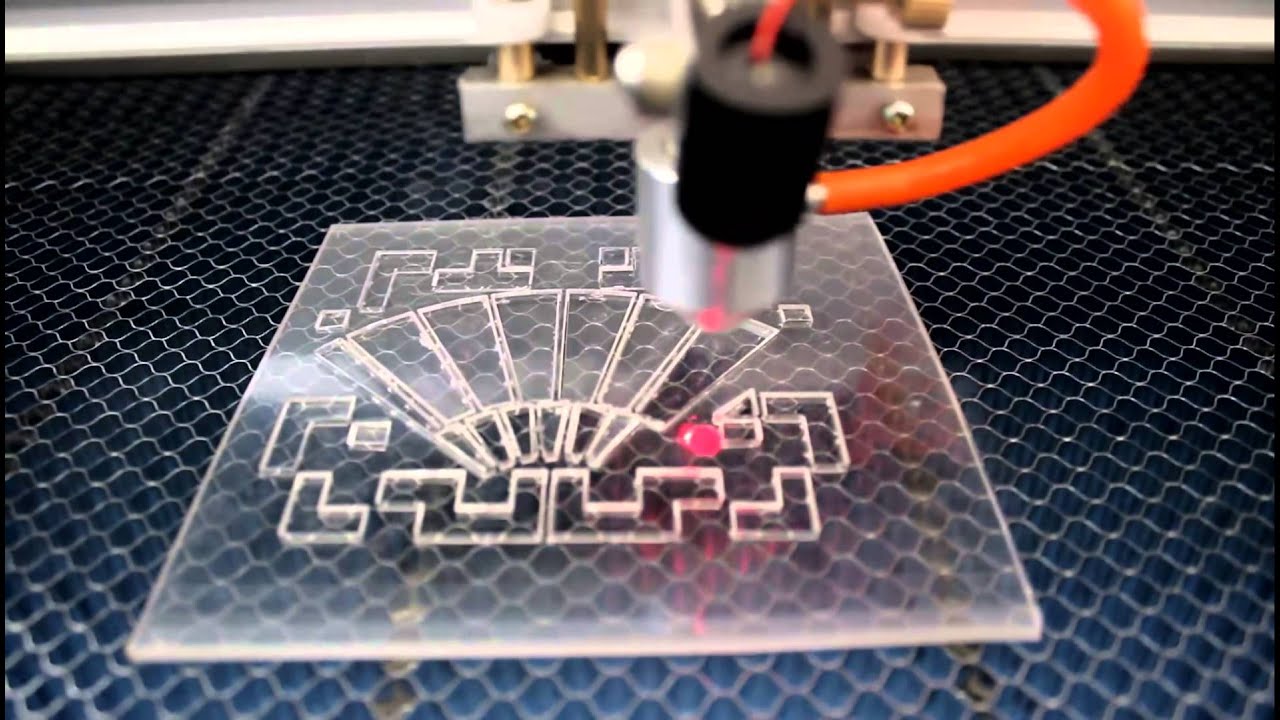
روش های برش لیزر
در ابتدا انواع مختلفی از لیزر ها با توجه به نحوه شکل گیری پرتو لیزر با استفاده از انواع مختلف پمپ های لیزری و رسانه های لیزری مورد بحث قرار گرفت. حال روش های برش لیزری را خواهیم دید که چگونه قطعات کوچک مواد برای ایجاد برش برداشته می شوند. چهار روش اصلی برش لیزری وجود دارد: تصعید، ذوب، واکنش و شکست تنش حرارتی.
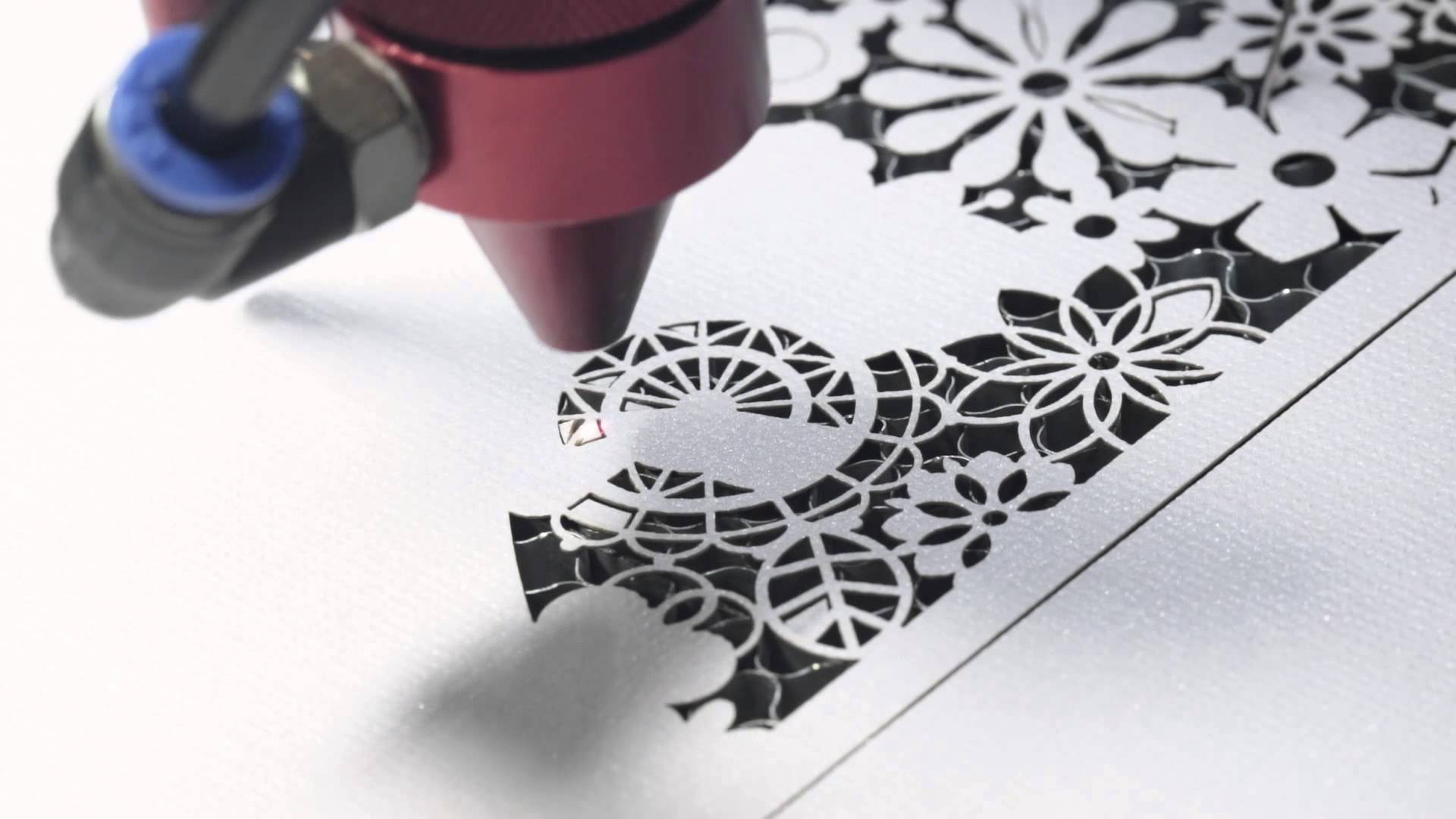
تصعید یا تبخیر
تصعید نوعی تغییر فاز از حالت جامد به حالت گازی بدون فاز مایع میانی است. این همان فرآیند تبدیل یخ خشک به بخار بدون تبدیل شدن به مایع است. این ماده به سرعت انرژی را جذب می کند که در آن هیچ شانسی برای ذوب شدن وجود ندارد. همین اصل برای برش لیزری نیز اعمال میشود، که در آن مقدار زیادی انرژی در زمان نسبتاً کوتاهی به ماده منتقل میشود که باعث تغییر فاز مستقیم ماده از حالت جامد به گاز و با کمترین ذوب شدن ممکن میشود. برش با ایجاد یک سوراخ اولیه یا شکاف شروع می شود. در شکاف، جذب بیشتری وجود دارد که باعث می شود مواد سریعتر بخار شود. این تبخیر ناگهانی یک بخار مواد با فشار بالا ایجاد می کند که بیشتر دیواره های شکاف را فرسوده می کند و مواد را از برش خارج می کند. این سوراخ یا برش را عمیق تر و بزرگتر می کند. این فرآیند برای برش پلاستیک، پارچه، چوب، کاغذ و فوم مناسب است که فقط به مقدار کمی انرژی برای بخار شدن نیاز دارد.
ذوب شدن
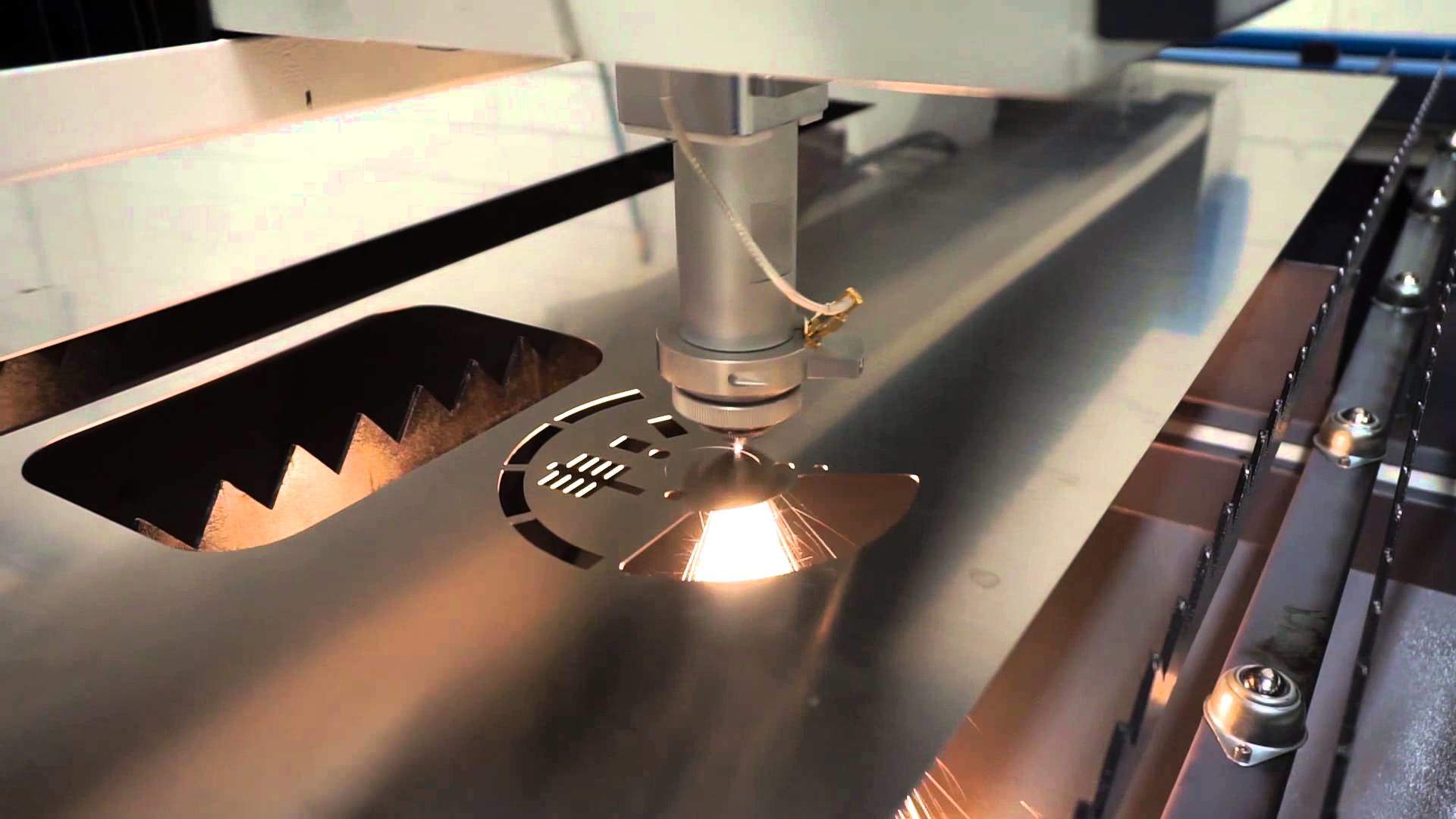
در مقایسه با تصعید، ذوب کردن به انرژی کمتری نیاز دارد. انرژی مورد نیاز حدود یک دهم از برش های لیزری است. در این فرآیند، پرتو لیزر مواد را گرم می کند، که باعث ذوب آن می شود. وقتی که مواد ذوب می شوند، یک جت گاز از نوز کواکسیال با پرتو لیزر مواد را از برش خارج می کند. گازهای کمک کننده استفاده شده بی اثر یا غیر واکنش هستند (به عنوان مثال، هلیوم، آرگون و نیتروژن) ، که تنها به برش از طریق وسایل مکانیکی کمک می کند. به دلیل نیاز کم به انرژی برای برش فلزات غیر اکسید کننده یا فعال مانند فولاد ضد زنگ، تیتانیوم و آلیاژهای آلومینیوم استفاده می شود.
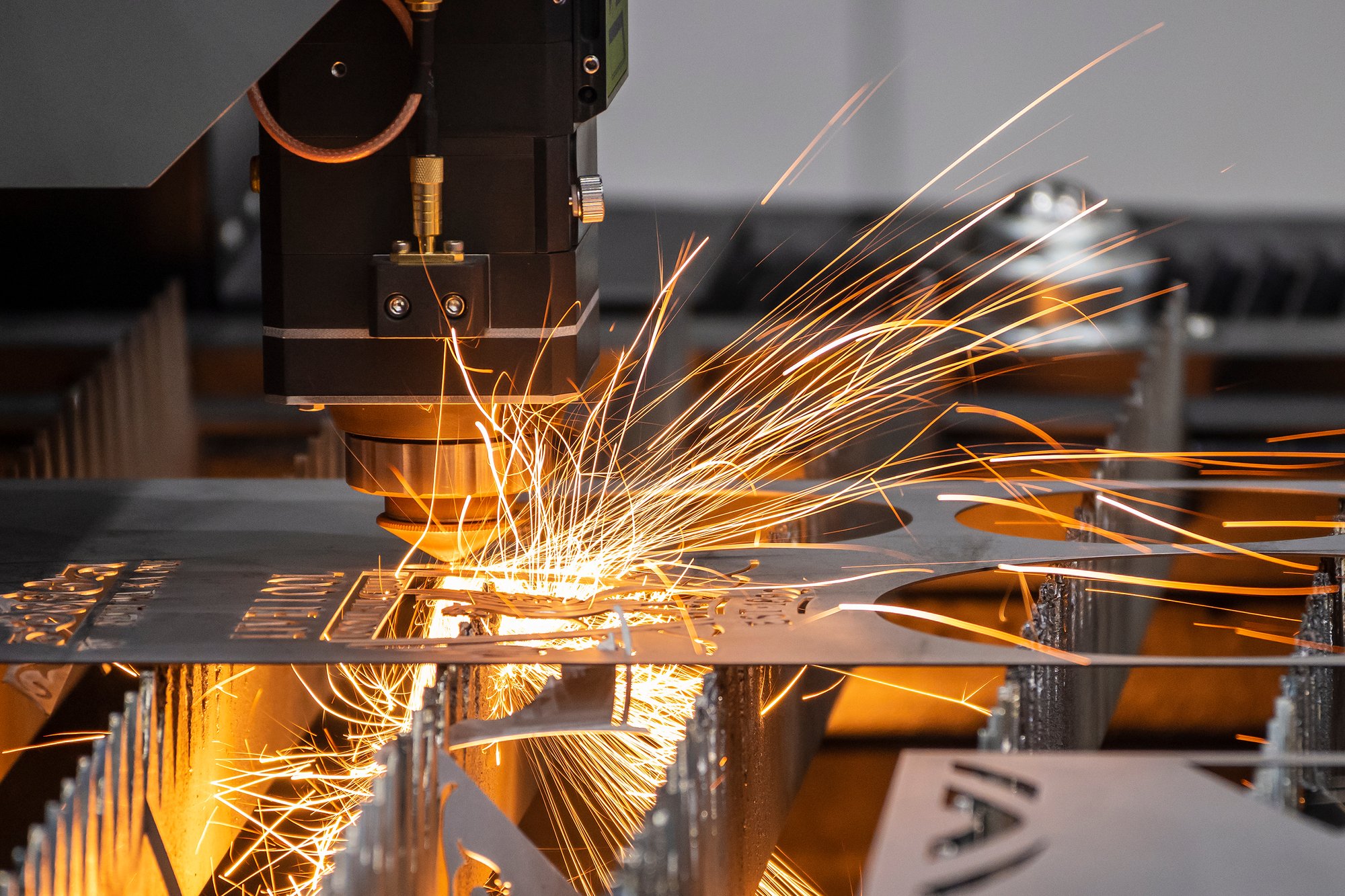
برش لیزری واکنش پذیر
در این فرآیند، از یک گاز واکنش پذیر برای تولید گرما با واکنش با مواد استفاده می شود. این فرآیند با ذوب کردن مواد با یک پرتو لیزر شروع می شود. وقتی که ماده ذوب می شود، یک جریان گاز اکسیژن از نازل هم محوری بیرون می آید و با فلز ذوب شده واکنش نشان می دهد. واکنش بین فلز و اکسیژن یک فرآیند اگزوترم است که به این معنی است که گرما آزاد می شود. این گرما به ذوب شدن مواد کمک می کند که حدود ۶۰٪ از کل انرژی مورد نیاز برای برش مواد است. اکسیدهای فلزی ذوب شده توسط فشار جت اکسیژن بیرون رانده می شوند. به غیر از انرژی کمتری که از پرتو لیزر مورد نیاز است ، سرعت برش با استفاده از گازهای واکنش پذیر سریعتر از برش لیزر با گازهای بی اثر است. با این حال ، از آنجا که این فرآیند به یک واکنش شیمیایی متکی است ، اکسید فلز ذوب شده که توسط جت اکسیژن استخراج نمی شود ، در امتداد لبه برش تشکیل می شود. این روش نسبت به استفاده از گاز های بی اثر، کیفیت پایین تر را تولید می کند. این فرآیند برای برش فولاد کربن ضخیم، فولاد تیتانیوم و سایر فلزات به راحتی اکسید شده استفاده می شود.
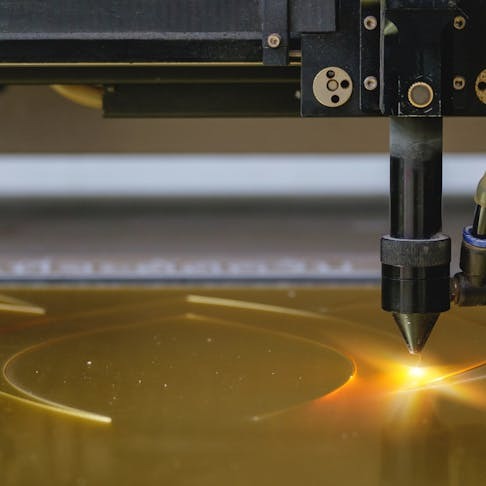